
OUR PRODUCTION PROCESS
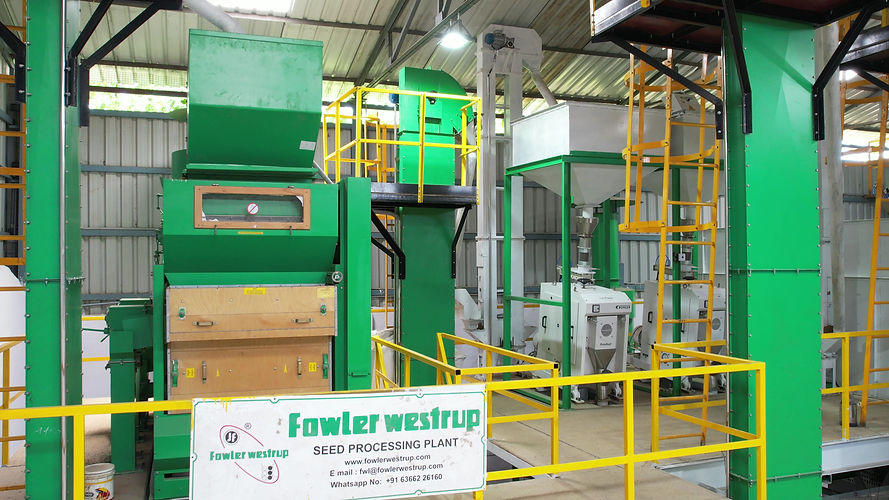
PREMIMINARY CLEANING
Pre - Cleaner removes impurities such as muds, dirt, sticks, plastic and other foreign matter from the raw - material. De - Stoner eliminates all the stones from the raw-material using gravity - separation.
HULLING & OIL TREATEMENT
The cleaned raw - material is passed through two hullers to create a perfect skin - scratch for oil-treatment. Split and dust are periodically removed using classifiers during hulling. Refined Sun - Flower Oil is used in Oil Addition in a controlled environment for De - Husking.
HEAT TREATMENT & WEATER ADDITION
After Oil Addition, the pulse is heat-treated up to 50°C for 4 hours and then let to cool for 48 hours.
HULLING & SECONDARY CLEANING
After 2 days of cooling, the pulse is hulled to remove the skin and then sent through cleaner and de - stoner to separate husk and dust particles from final product.
Color - Sorting & Packing
3D imaging color sorter is used to color grade and eliminate unprocessed pulse
COLOUR SORTING & PACKING
3D imaging color sorter is used to color grade and eliminate unprocessed pulse from the final product. Packing is done to suit the buyer's requirement ranging from 5Kg pouches to 50 Kg Bags.